Hannoversche Grubenholzindustrie Nachf. Voigtländer & Hinze
|
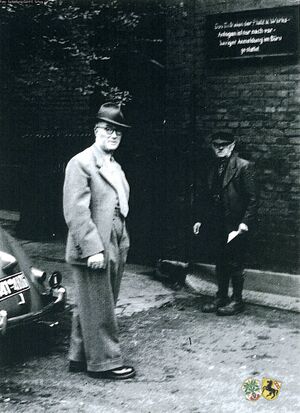
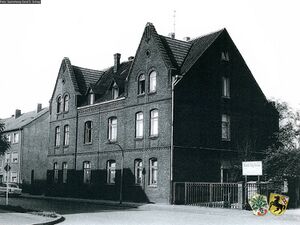
Die Herren Voigtländer und Hinze, als Nachfolger der Hannoversche Grubenholzindustrie Meyer & Fröhlich, brachten mit geschäftlicher Weitsicht das Sägewerk zu großer Blüte. Man Erkannte, daß ein guter und erfolgreicher Geschäftsweg die Spezialisierung ist. Das Geschäft mit normalem Grubenholz (sprich Grubenstempel) wurde von vielen Holzhändlern und Waldbesitzern betrieben. Die Spezialisierung auf ein Haupt-Produktzweig versprach größeren geschäftlichen Erfolg. So konzentrierte man sich auf die Produktion von Schachtholz. Unter diesem Begriff sind die für den Schachtbau (und deren permanenter Reparatur) benötigten schweren Eichenbalken zu verstehen. Die bergmännischen Begriffe dafür sind Einstriche und Spurlatten.
Da diese Spezialhölzer ausschließlich aus Eiche bestanden und aufgrund der hohen Sicherheitsansprüche große Qualität vorgeschrieben war, wurde man zum Spezialversorger. Im näheren Umkreis war nur noch das frühere Sägewerk in Castrop-Rauxel (ein Tochterunternehmen der Vereinigten Holzgesellschaften in Essen) auf diesem Gebiet tätig. Diese beiden Firmen unterhielten gute Geschäftsbeziehungen. Man half sich in dringenden Fällen – oder Notsituationen auf den Zechen – gegenseitig.
Selbstverständlich wurden im Sägewerk auch andere Hölzer verarbeitet, die an örtliche Schreinereien, Tischlereien, Dachdecker, Sarghersteller u.s.w. verkauft wurden. Die waren in der Regel Kanthölzer, Bretter, Bohlen, Latten u.s.w.
Für die Produktion standen in dem großen Sägehaus
- zwei Vollgatter, Fabrikat Esterer,
- ein Horizontalgatter, Fabrikat Wurster,
- eine große Bandsäge,
- und diverse Kreissägen
zur Verfügung.
Alle diese Sägen wurden mittels einer großen Dampfmaschine (mit einem riesengroßen Schwungrad) über ein unterirdisches System von Treibriemen angetrieben. Lediglich die zusätzlich vorhandenen Maschinen außerhalb des Sägehauses (Kreissägen, Bandsägen etc.) wurden mit Strom betrieben.
Jeden Montag ab 5.00 Uhr wurde die Dampfmaschine von dem Maschinenführer (Herr Ehser) angeheitzt. Interessant und äußerst erwähnenswert ist, daß die große Dampfmaschine ausschließlich mit den im Sägewerksbetrieb anfallenden Holzresten, Spänen, Rinden, Sägemehl etc. betrieben wurden. Es kamen keine anderen Brennstoffe (wie z. B. Kohle, Koks, Öl o. ä.) zum Einsatz. Eine externe Abfallentsorgung gab es nicht und war auch nicht erforderlich.
Die Dampfmaschine war so leistungsfähig, daß sie auch den im Betrieb benötigten Strom für Beleuchtung etc. (in 110 Volt) voll selbst erzeugte. Auch das benötigte heiße Wasser für Heizung und Duschen in den Sozialräumen sowie für den Betrieb der Imprägnieranlage lieferte die Dampfmaschine. Man war sozusagen in der Energieversorgung autark.
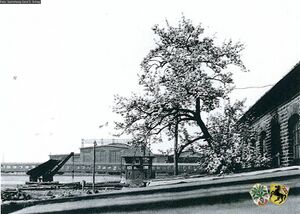
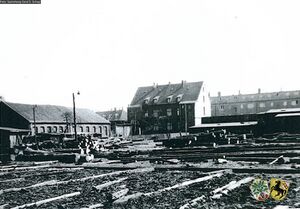
Das Firmengelände gliederte sich in folgende Bereiche:
- Rundholzplatz mit Bahnanschluß und Verladekran (handbetrieben),
- Sägehalle (zwei Vollgatter, ein Horizontalgatter, eine große Bandsäge und diverse Kreissägen),
- vier Lager- und Trockenschuppen für Schnittholz
- Schnittholz-Lagerplatz,
- Sägenschärferei (Herr Prinz),
- Betriebswerkstatt und Sozialräume und
- Bürogebäude.
In einem der Trockenschuppen befand sich ausschließlich wertvolle Blochware (Blockware). Dies waren sorgfältig gesägte Baumstämme (Eiche, Buche, Kirsche, Birne, Lärche, Ulme, Ahorn, Esche, Linde etc.) die nach dem Schnitt wieder als Stamm (Block) zusammengestellt wurden. Es kamen lediglich Stapelplatten dazwischen, damit die Bohlen besser trocknen konnten. Eine Faustzahl besagte: Pro cm Dicke = ein Jahr Lufttrocknung. Da die Bohlen in der Regel 5 cm bzw. 8 cm dick waren, kann man die Lagerdauer gut ermitteln.
Diese Bohlen (mit Rinde versehen) waren bei Schreinern, Tischlern, Stellmachern u.s.w. hoch begehrt, da das Holz nach der Verarbeitung nicht mehr arbeitete, d. h. sich nicht mehr verzog.
Eine Spezialität war auch die Produktion von Holzpflaster für Werkstätten und Fabrikhallen. Die Böden in den Hallen und Werkstätten der damaligen Zeit wurden in der Regel mit Holzpflaster ausgelegt. Dieser Bodenbelag war robust, lärmmdämmend, widerstandsfähig gegen höchste Belastung und hatte eine nahezu unbegrenzte Lebensdauer. Außerdem war dieser Bodenbelag für die Mitarbeiter angenehm fußwarm. Das Holzpflaster war 80 x 80 mm (Höhe/Breite) und zwischen 120 mm und 200 mm lang. Es wurde mit heißem Steinkohlenteeröl imprägniert und stirnseitig verlegt.
Die für den Sägebetrieb benötigten Baumstämme (sogenanntes Langholz) wurde täglich per LKW oder Eisenbahn-Rungenwagen angeliefert. Es war nicht immer einfach, die für die Schachthölzer geeigneten Eichenstämme in ausreichender Menge zu beschaffen. Insofern musste auf dem Rundholzplatz ein ausreichender Vorrat vorhanden sein, damit die Produktion aufrecht gehalten werden konnte. Man konnte auch nur bedingt auf Vorrat schneiden, da die meisten Schachteinbauten ganz individuelle Maße hatten. Die Einteilung für den Einschnitt war wissenschft für sich. Herr Heyna war da Spezialist mit jahrzente langer Erfahrung.
Das bevorzugte Einkaufsgebiet für die Eichenstämme waren Sauerland, Westerwald, Eifel, Bergisches Land und der Niederrhein — auch wegen der Transportkosten.
Die Stämme vom Niederrhein waren nur bedingt nutzbar, da hier (z. B. Rundholz aus dem Reichswald) oft starker Splitterbefall (Granatsplitter) aus den Kämpfen des 2. Weltkrieges in den Bäumen steckte, was man nur schwerlich sehen konnte.
Wenn so ein Splitterstamm unentdeckt durch ein Sägegatter gezogen wurde, konnte es passieren, daß die Sägeblätter alle Sägezähne verloren und diese als Eisensplitter durch die Sägehalle flogen. Verletzungen waren dann oft die Folge. Für die betriebseigene Sägenschärferei (Herr Prinz) war dann Hochbetrieb angesagt.
Vor, während und kurz nach dem 2. Weltkrieg wurden die Baumstämme zum Teil von eingenen Mitarbeitern, die von Montag bis Samstag in den Wäldern tätig waren, gefällt, gerückt und aufgearbeitet. Dafür hatte man Wohnwagen, ähnlich den später noch bekannten Bauwagen. Einer dieser Wohn-/Bauwagen stand immer noch auf dem Rundholzplatz und diente einem Mitarbeiter (Herr Ambrassat) als Wohnung. Er war einer der besten, zuverlässigsten und fleißigsten Arbeiter. Er arbeitete von Sonnenaufgang bis Sonnenuntergang und hielt sich nicht an Arbeitszeitvorgaben.
Wenn man einige der damals belieferten Zechen aufzählt, dann sind die Namen heutzutage für viele unbekannt oder Historie:
- Zeche Holland,
- Zeche Minister Stein,
- Zeche Adolph von Hansemann,
- Zeche Hansa,
- Zeche Westhausen,
- Zeche Beekerwerth,
- Zeche Dahlbusch und
- Zeche Bonifacius.
Beschäftigt wurden immer um die 40 Mitarbeiter, wobei während des 2. Weltkriegs zusätzlich viele Fremdarbeiter (insbesondere Roma) arbeiteten. Der Betrieb war während des Krieges als kriegswichtig eingestuft, um die Produktion von Kohle aufrecht zu erhalten. Nutznießer dieser Einstufung war auch ein Teil der Belegschaft, da die Spezialisten (Gatterfüher etc.) vom Wehrdienst befreit waren. Auch der technische Leiter des Betriebes, Herr Fehlau, (die 'Seele des Betriebes') war vom Wehrdienst befreit gewesen.
Der Verfasser dieses Artikels hat es in den 1950er Jahren noch selbst wiederholt erlebt, daß ehemalige Fremdarbeiter im Büro vorstellig wurden und um einen Nachweis für ihre Tätigkeit nachsuchten. Da ein gut geführtes Mitarbeiterbuch vorlag, konnte in der Regel der schriftliche Nachweis gegeben werden.
Eine besondere Blütezeit war die Zeit nach dem 2. Weltkrieg, da hier die Produktion von Kohle in Deutschland oberste Priorität hatte. Man weiß heute, daß der Bergbau „das“ Standbein des sogenannten Wirtschaftswunders war.
Mit dem Zechensterben Ende der 1950er Jahre kamen auch die Probleme auf das Sägewerk zu. Als dann 1958 die nebenan beheimatete Maschinenfabrik Beien dringend Gelände für eine Betriebserweiterung benötigte, entschloß man sich zur Aufgabe des Sägewerks und zum Teilverkauf des Geländes an die Firma Beien.
Damit war das über 70 Jahre alte Dampf-Sägewerk in Herne geschichte.
Lediglich der Holzhandel lief unter neuem Namen Weiter. [2]
Verwandte Artikel
- Arnold Voigtländer Holzgroßhandlung (← Links)
- Tätigkeitsbericht 1 des Lehrlings Gerd Schug (← Links)
- Gerd E. Schug (← Links)